Nordic Semiconductor has been a provider of integrated electronics designs, products and related services since 1983. Due to the inherent complexity of integrated device design and manufacturing, assuring that the deliverables are according to our customer’s expectations has always been an integral part of our workflow.
Nordic Semiconductor designs and develops our own products which are manufactured by subcontractors, and sold globally through distribution partners, as shown in the value chain illustration below. To enhance the developers' experience and speed up our customers' design cycles, we also develop and provide related products and services, such as software, applications and tools.
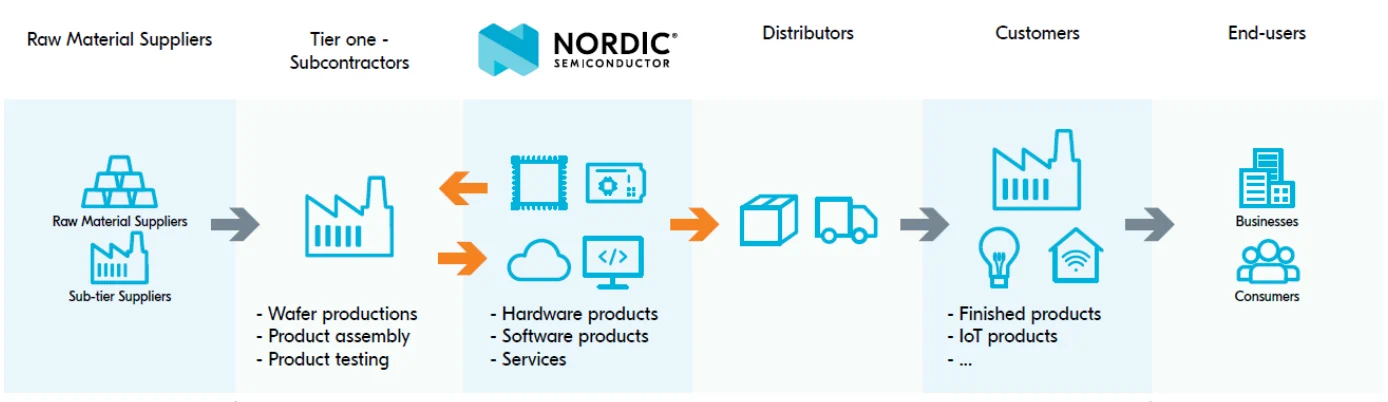
Company Vision |
Business Idea |
Quality Policy |
---|---|---|
Simplified lives through all things connected. Things ...we wear ...we carry around ...around us at home ...around us at work ...around us in the city ...around us in the countryside
A leading vendor of wireless connectivity and embedded processing solutions for internet connected things with a sustainable footprint.
|
Develop, sell, and deliver integrated circuits and related products and services - Define our own products, driven by market demands and opportunities - Offer customer defined, standardized solutions - Produce components using world class manufacturing subcontractors - Enable and encourage socially- and environmentally sustainable customer solutions - Sell and market our products worldwide through:
|
Profitability and customer satisfaction at the same time: - Deliver the right product on time and without defects to get satisfied customers and partners - Communicate clearly and timely to put expectations right - Comply with applicable standards and regulations - Work continuously to reduce waste in our processes |
Nordic Semiconductor work continuously to improve our products and services, and to ensure adherence to the highest possible standards. The company’s quality management system has been certified to ISO 9001 since 1996. The main drivers of our Quality Management System are our defined policies, like the company vision, business idea and quality policy.
To keep up with the pace of the evolving electronics industry, process orientation, risk management and non-conformance methodology is essential. Nordic Semiconductor is organized according to the main processes of our business, and the processes are assigned dedicated «process owners» responsible for improvements.
Design projects are managed through a risk-oriented approach and every design sub-process ends with a review with a corresponding checklist and a reference team to assure the quality of the deliverables. Advanced verification tools and methods are important parts of the design processes. Essential outputs from the development process include accurate quality and manufacturing instructions for our manufacturing partners.
Nordic has implemented well-defined processes to ensure that our products are qualified to applicable standards, hereunder JEDEC JESD-47 for reliability, teleregulatory standards like RED and FCC, and communication protocol standards like the Bluetooth standard.
Fabless quality management
As a fabless semiconductor company, supply chain management is a vital part of our activity. For wafer processing, assembly, and test, we have chosen world class manufacturing partners.
Nordic Semiconductor has a dedicated Supply Chain department, responsible for managing the company’s manufacturing partners and their performance. Initial evaluation, including auditing, of suppliers is performed to ensure that they satisfy quality requirements and perform professional delivery. All Nordic’s manufacturing partners are certified to the standards ISO 9001, ISO 14001, ISO 45001, as well as to various automotive and environmental standards.
A vital part of the supply chain management is to ensure business continuity through multi-sourcing options and material buffering strategies.
Nordic’s Supply Chain department conducts regular supplier audits and follow-up of audit results to improve supplier performance on topics related to quality, environmental management, and social responsibility. Normal operational routines include addressing targets and deadlines with suppliers and organizing business reviews at defined frequencies.
Change management
Nordic Semiconductor’s main obligation is to deliver components that are working according to the Product Specification. A change to the product or the manufacturing process that can adversely affect the specification or the reliability of the product is notified to the customers with a Product Change Notification (PCN). Triggers for PCN may be a change in a subcontractor process, inclusion of second source suppliers, redesign as a result of failure analysis, changed sampling plans, etc. Requirements for re-qualification and verification activities are defined to reflect the scope and risk of the change. Nordic’s issuance of PCN’s follow the JEDEC standard J-STD-46, and notifications are distributed within 90 days of a scheduled shipment.
Similarly, a product’s end of life is notified with a Product Discontinuance Notice (PDN). General guidelines for PDN’s are given in JEDEC standard J-STD-48, and notification of direct customers and distributors are given within 6 months of last order date and 12 months of last shipment date. Nordic Semiconductor has issued a Long-term parts availability statement that describes criteria for product discontinuance.
Published PCNs, PDNs, and other Informational Notices can at all times be found in Nordic’s Infocenter.
Failure analysis and RMA process
Nordic Semiconductor Technical Support is available for all customers through the DevZone portal. DevZone is Nordic Semiconductor’s preferred communication channel for customers support, as this allows for secure information exchange. Suspected failures or issues related to quality and/or reliability can be reported through the DevZone portal.
Purchased goods can only be returned after being authorized by Nordic Semiconductor with a Return Material Authorization (RMA). This document (or its ID) shall always follow the returned material and related correspondence to assure correct handling. The case handling is organized according to the 8-Discipline problem solving methodology. In order to reduce case handling time and achieve higher success rate for root cause analysis, Nordic Semiconductor operates a well-equipped Failure Analysis lab. The lab is also an efficient service provider for debugging and design analyses during the development and qualification stages of new products.